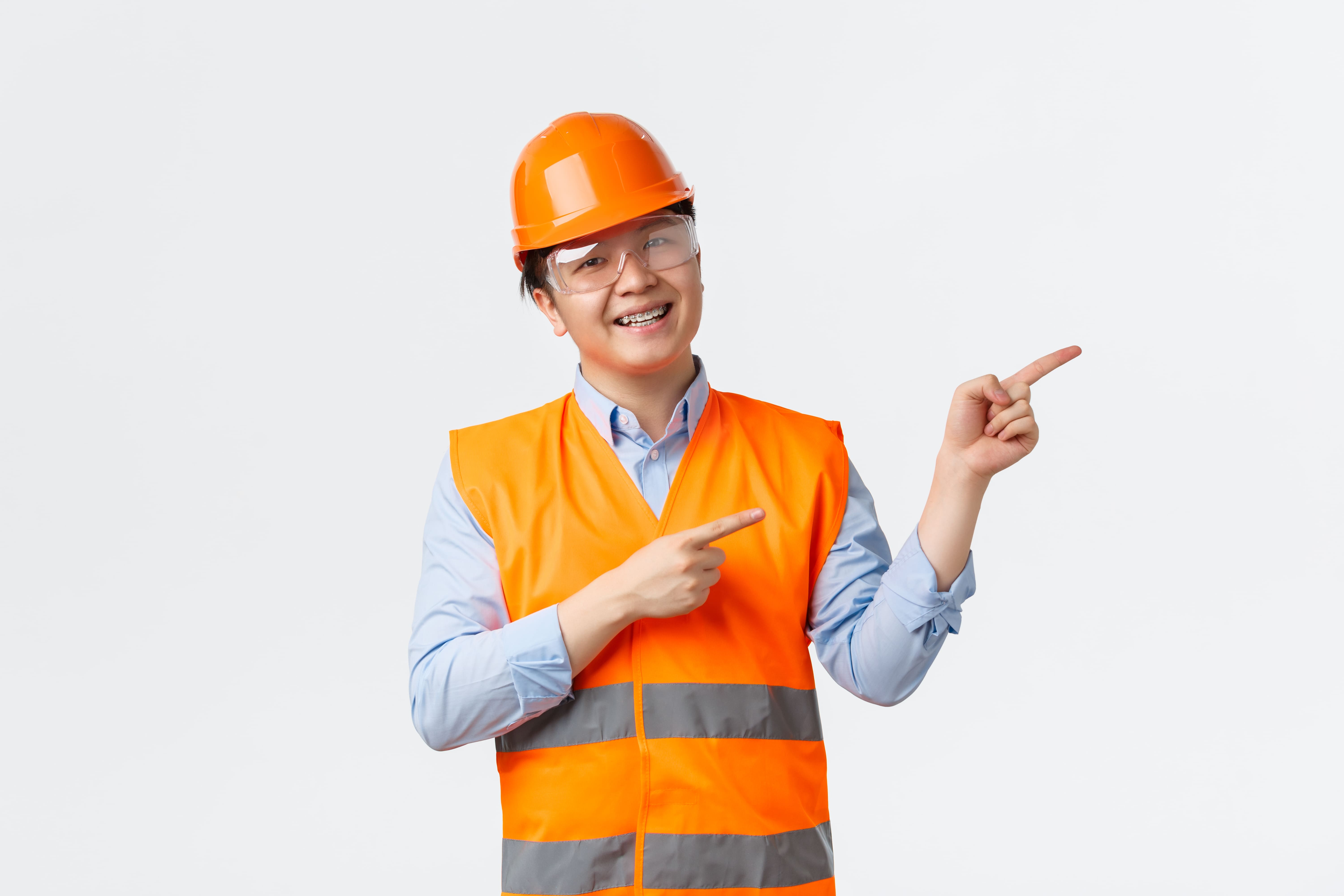
Pentingnya Manajemen Fatigue di Perusahaan Tambang dan Regulasi Kecukupan Jam Tidur
Occupational Health and Safety (OHS) management is a critical component of any organization’s strategy to ensure the well-being of its employees, compliance with legal requirements, and the overall productivity of its operations. In today’s business environment, where workplace hazards can vary widely across different industries, a comprehensive OHS management system is essential. This article explores the importance of OHS management, its key components, and best practices for implementing an effective OHS program within a company.
The Importance of OHS Management
Protecting Employee Well-Being
The primary goal of OHS management is to protect the health and safety of employees. Ensuring a safe working environment reduces the risk of accidents and injuries, which in turn decreases absenteeism and improves overall employee morale and productivity. Healthy and safe employees are more likely to perform their duties efficiently and contribute positively to the company’s success.
Legal and Regulatory Compliance
Companies are legally required to comply with occupational health and safety regulations. Non-compliance can result in severe penalties, legal liabilities, and damage to the company’s reputation. A robust OHS management system helps organizations adhere to these regulations, thus avoiding legal repercussions and maintaining their standing as responsible employers.
Enhancing Productivity and Efficiency
A well-implemented OHS management system minimizes workplace disruptions caused by accidents and illnesses. This leads to smoother operations, fewer work stoppages, and reduced costs associated with injuries and health-related absences. By fostering a culture of safety, companies can enhance productivity and operational efficiency.
Key Components of OHS Management
Hazard Identification and Risk Assessment
Identifying potential hazards and assessing associated risks is the foundation of an effective OHS management system. This involves:
Workplace Inspections: Conducting regular inspections to identify hazards in the work environment.
Risk Assessments: Evaluating the likelihood and severity of identified hazards to prioritize risk mitigation efforts.
Incident Reporting: Encouraging employees to report near-misses and unsafe conditions to proactively address potential risks.
Development of Safety Policies and Procedures
Clear and comprehensive safety policies and procedures provide guidelines for safe work practices. These should include:
Standard Operating Procedures (SOPs): Detailed instructions on how to safely perform specific tasks.
Emergency Response Plans: Procedures for dealing with emergencies such as fires, chemical spills, and medical incidents.
General Safety Rules: Basic safety rules that all employees must follow, such as the use of personal protective equipment (PPE) and adherence to safe work practices.
Employee Training and Education
Training and educating employees on safety practices is crucial for creating a safety-conscious culture. Effective training programs should include:
Induction Training: Initial training for new employees covering basic safety procedures and company policies.
Ongoing Training: Regular refresher courses and updates on new safety practices and regulations.
Specialized Training: Training for specific high-risk activities or the use of specialized equipment.
Monitoring and Evaluation
Continuous monitoring and evaluation are essential for maintaining and improving safety standards. This involves:
Safety Inspections: Regular inspections to ensure compliance with safety policies and identify new hazards.
Incident Reporting Systems: Efficient systems for reporting accidents, near-misses, and unsafe conditions.
Data Analysis: Analyzing safety data to identify trends, assess the effectiveness of safety measures, and make informed decisions.
Best Practices for Implementing an Effective OHS Program
Leadership Commitment and Involvement
The success of any OHS management system depends on the commitment and involvement of leadership. Senior management must prioritize safety, allocate necessary resources, and lead by example. This includes:
Setting Safety Goals: Establishing clear and achievable safety objectives.
Allocating Resources: Providing the necessary funding, personnel, and equipment for safety initiatives.
Leading by Example: Demonstrating a commitment to safety by following safety protocols and encouraging a safety-first culture.
Employee Engagement and Participation
Engaging employees in safety initiatives fosters a sense of ownership and responsibility. Strategies for enhancing employee participation include:
Safety Committees: Forming safety committees comprising employees from various levels to discuss safety issues and recommend improvements.
Incentive Programs: Implementing reward systems for employees who consistently follow safety protocols and contribute to a safe working environment.
Feedback Mechanisms: Encouraging employees to provide feedback on safety practices and report potential hazards.
Continuous Improvement and Regular Reviews
OHS management is an ongoing process that requires continuous improvement and regular reviews. This involves:
Periodic Reviews: Conducting regular reviews of safety policies, procedures, and performance.
Audits and Assessments: Performing internal and external audits to evaluate the effectiveness of the OHS management system.
Continuous Improvement: Using insights gained from reviews and audits to make continuous improvements to safety practices and protocols.
Leveraging Technology
Advancements in technology offer innovative solutions for enhancing OHS management. Key technological tools include:
IoT and Wearables: Utilizing IoT devices and wearable technology to monitor environmental conditions and workers’ health in real time.
Safety Management Software: Implementing software solutions for tracking incidents, managing safety data, and ensuring compliance with regulations.
Automation and Robotics: Integrating automation and robotics to perform high-risk tasks, thereby reducing human exposure to hazards.
Challenges in OHS Management
Resource Constraints
Implementing a comprehensive OHS management system can be resource-intensive, requiring significant investment in time, money, and personnel. Smaller companies may face challenges in allocating sufficient resources for effective OHS management.
Changing Regulations
Occupational health and safety regulations can change frequently, requiring companies to stay updated and ensure compliance. Keeping up with these changes can be challenging, especially for companies operating in multiple jurisdictions.
Employee Resistance
Employees may resist changes to established work practices, particularly if they perceive new safety measures as burdensome or unnecessary. Overcoming this resistance requires effective communication and engagement strategies.
Case Studies and Success Stories
Case Study 1: Manufacturing Industry
A manufacturing company implemented a comprehensive OHS management system that included regular safety audits, advanced training programs, and the use of IoT devices to monitor environmental conditions. As a result, the company saw a significant reduction in workplace accidents and improved overall safety performance. The success of the program was attributed to strong leadership commitment, employee engagement, and the effective use of technology.
Case Study 2: Construction Industry
A construction firm faced challenges with frequent machinery accidents and downtime. By adopting an OHS management system that emphasized preventive maintenance, regular safety training, and the use of automated safety checks, the company managed to reduce accidents and increase productivity. The key to their success was the integration of safety protocols into everyday operations and continuous monitoring and improvement.
Conclusion
Occupational Health and Safety management is essential for protecting employees, ensuring legal compliance, and enhancing productivity within companies. By identifying hazards, developing comprehensive safety policies, engaging employees, and leveraging technology, organizations can create a safe working environment and foster a culture of safety. Continuous improvement and strong leadership commitment are crucial for maintaining high safety standards and achieving long-term success. Investing in robust OHS management systems not only safeguards employees but also contributes to the overall growth and sustainability of the organization.
Pentingnya Manajemen Fatigue di Perusahaan Tambang dan Regulasi Kecukupan Jam Tidur
Bahaya Kelelahan di Lingkungan Kerja: Faktor Penyebab dan Solusinya
Kecelakaan Kerja Akibat Fatigue: Pengertian, Penyebab, dan Solusi Pencegahannya
Peran Fatigue Management dalam Mengurangi Risiko Kecelakaan Akibat Mengantuk
Pentingnya Manajemen Fatigue di Perusahaan Tambang dan Regulasi Kecukupan Jam Tidur
Bahaya Kelelahan di Lingkungan Kerja: Faktor Penyebab dan Solusinya
Kecelakaan Kerja Akibat Fatigue: Pengertian, Penyebab, dan Solusi Pencegahannya
Peran Fatigue Management dalam Mengurangi Risiko Kecelakaan Akibat Mengantuk