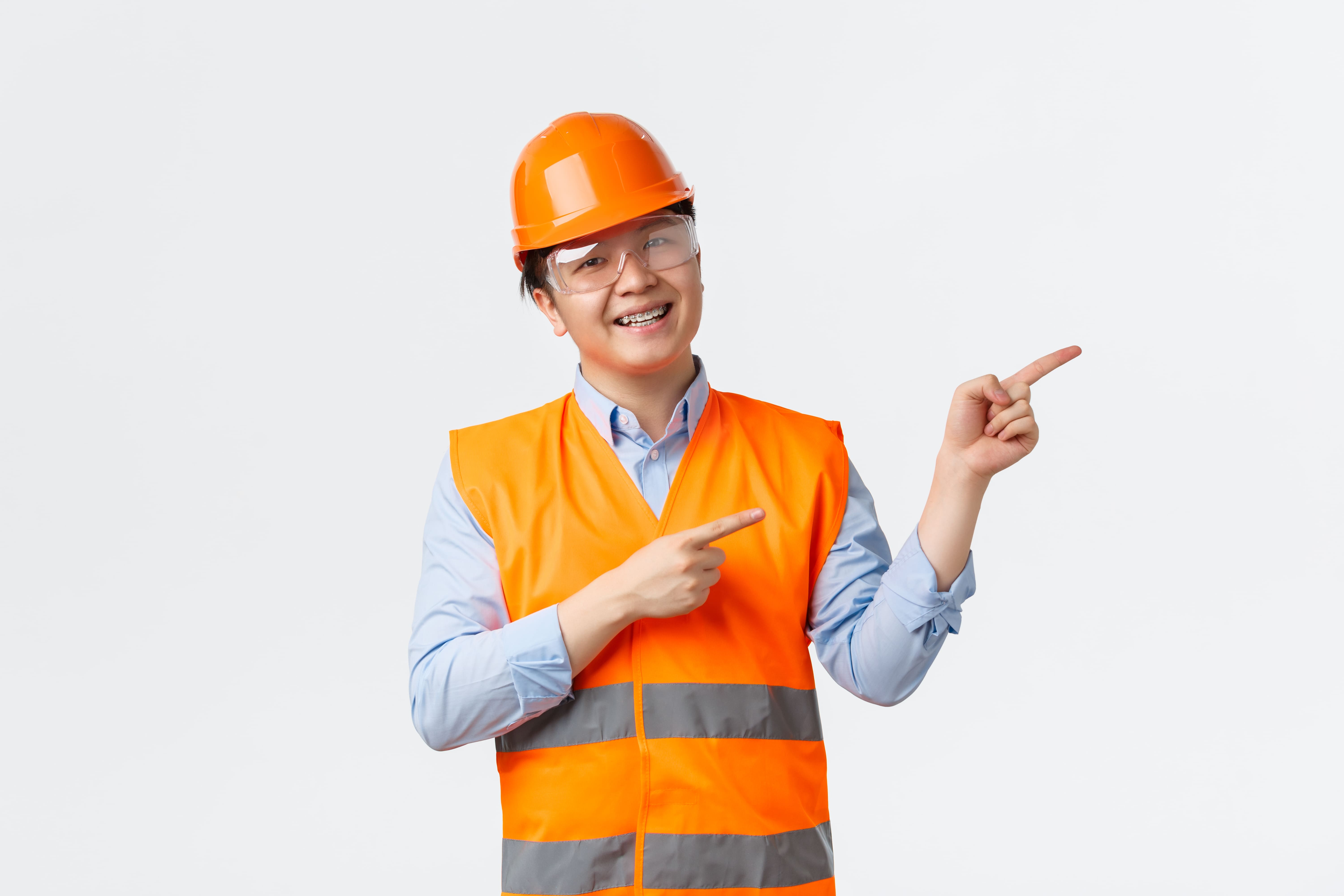
Pentingnya Manajemen Fatigue di Perusahaan Tambang dan Regulasi Kecukupan Jam Tidur
Why Is Workplace Safety Important?
Workplace safety is a crucial aspect in any work environment, particularly in high-risk industries such as mining, manufacturing, construction, and transportation. Workplace accidents can lead to serious injuries or even fatalities and can financially harm the company through worker compensation, repair costs, and lost productivity. Therefore, efforts to maintain workplace safety must be a top priority, one of which is through the implementation of safety support systems.
Necessary Safety Support Systems in the Workplace
To create a safe work environment, companies need to implement various safety support systems specifically designed to reduce the risk of accidents and ensure worker well-being. Here are some essential systems:
Occupational Health and Safety Management System (OHSMS) OHSMS is a framework designed to manage safety and health risks in the workplace. This system includes policies, procedures, and best practices that companies must apply to ensure that all aspects of worker safety and health are met. OHSMS also involves regular audits and continuous training to ensure that safety standards remain high.
Hazard Monitoring and Detection Systems In high-risk work environments, hazard monitoring and detection systems are vital components. These systems can include various technologies, such as toxic gas detection sensors, fire alarm systems, and air quality monitors. These tools are designed to detect potential hazards in real-time and provide early warnings to workers so that preventive measures can be taken immediately.
Ergonomic Risk Control Systems Workplace accidents are often caused by ergonomic issues, such as improper work positions, unsuitable equipment, or excessive repetitive movements. Ergonomic risk control systems help analyze jobs and the equipment used to ensure that they do not cause injury to workers. This can include adjusting workstations, training on proper posture, and using ergonomic aids.
Safety Training and Education Systems Regular and in-depth safety training is crucial to ensure that workers understand the risks in the workplace and know how to address them. Safety training systems include modules on emergency procedures, the use of personal protective equipment (PPE), and rescue and first aid techniques. These training programs should be tailored to the specific needs of the industry and the jobs being performed.
Incident Management and Accident Reporting Systems This system serves to record, analyze, and report any incidents or accidents that occur in the workplace. With the data collected, companies can identify patterns or trends that require special attention and take necessary corrective actions to prevent similar accidents in the future. This system is also important for compliance with government regulations and industry standards.
Worker Health Monitoring Systems In addition to safety monitoring, it is also important to monitor workers' health, especially for those working in physically demanding conditions or long shifts. This system may include regular health check-ups, physical condition monitoring through wearable devices, and employee wellness programs that include stress management and mental health support.
Environmental Management Systems Environmental management systems are designed to ensure that company activities are not only safe for workers but also do not harm the surrounding environment. This includes the management of hazardous waste, pollution control, and environmental conservation efforts. By keeping the environment safe and healthy, the risks faced by workers can also be minimized.
Technological Innovations in Safety Support Systems
With technological advancements, many safety support systems now rely on cutting-edge technology to improve efficiency and effectiveness in maintaining workplace safety. Significant technological innovations include:
Fatigue Management System
One of the most important innovations in workplace safety is the implementation of the Fatigue Management System. This system is designed to monitor worker fatigue levels and prevent accidents caused by fatigue. Using wearable devices equipped with sensors, the Fatigue Management System can detect signs of fatigue, such as abnormal heart rates, poor sleep patterns, or decreased concentration. This information is then sent to a control center, allowing management to take proactive actions, such as providing additional rest or reassigning workers to lighter tasks.
Internet of Things (IoT) in Workplace Safety
IoT enables the integration of various devices and sensors to monitor work conditions in real-time. For example, temperature sensors, gas detectors, and wearable devices can be connected to a control center that continuously monitors worker safety. The data collected can also be analyzed to predict potential hazards and anticipate risks before they occur.
Augmented Reality (AR) for Safety Training
AR can be used in safety training to provide realistic and interactive simulations. Workers can practice in hazardous situations virtually, helping them understand how to react in emergency conditions without the risk of injury.
Wearable-Based Fatigue Monitoring Systems
Wearable devices integrated with fatigue monitoring technology allow companies to track workers' physical conditions in real-time. This is crucial in preventing fatigue that could lead to workplace accidents, especially in industries requiring high concentration or heavy physical labor.
SmartSafety: The Ultimate Solution in Fatigue Accident Prevention
One of the biggest challenges in maintaining workplace safety is managing worker fatigue. Fatigue can lead to decreased concentration, slow reactions, and judgment errors, all of which can increase the risk of workplace accidents. While various safety support systems can be implemented, the most powerful technology in preventing fatigue-related accidents is the Fatigue Management System like SmartSafety.
SmartSafety uses advanced IoT technology and wearable devices to monitor worker fatigue levels in real-time. This device can detect signs of fatigue, such as changes in heart rate patterns or poor sleep quality, and provides early warnings to workers and management. With SmartSafety, companies can take preventive measures, such as providing additional rest or task adjustments, before fatigue reaches a dangerous level.
SmartSafety has proven effective in preventing fatigue-related accidents at dozens of sites in Indonesia and has been used by thousands of workers. By leveraging this technology, companies can ensure that their workers remain in optimal physical and mental condition, thereby minimizing the risk of workplace accidents.
Workplace safety is a priority that cannot be ignored in high-risk work environments. By implementing various safety support systems, including safety management, hazard monitoring, training, and technological innovations, companies can create a safe and productive work environment. Moreover, using a Fatigue Management System like SmartSafety, companies can proactively prevent fatigue-related accidents and ensure the well-being of their workers.
Pentingnya Manajemen Fatigue di Perusahaan Tambang dan Regulasi Kecukupan Jam Tidur
Bahaya Kelelahan di Lingkungan Kerja: Faktor Penyebab dan Solusinya
Kecelakaan Kerja Akibat Fatigue: Pengertian, Penyebab, dan Solusi Pencegahannya
Peran Fatigue Management dalam Mengurangi Risiko Kecelakaan Akibat Mengantuk
Pentingnya Manajemen Fatigue di Perusahaan Tambang dan Regulasi Kecukupan Jam Tidur
Bahaya Kelelahan di Lingkungan Kerja: Faktor Penyebab dan Solusinya
Kecelakaan Kerja Akibat Fatigue: Pengertian, Penyebab, dan Solusi Pencegahannya
Peran Fatigue Management dalam Mengurangi Risiko Kecelakaan Akibat Mengantuk