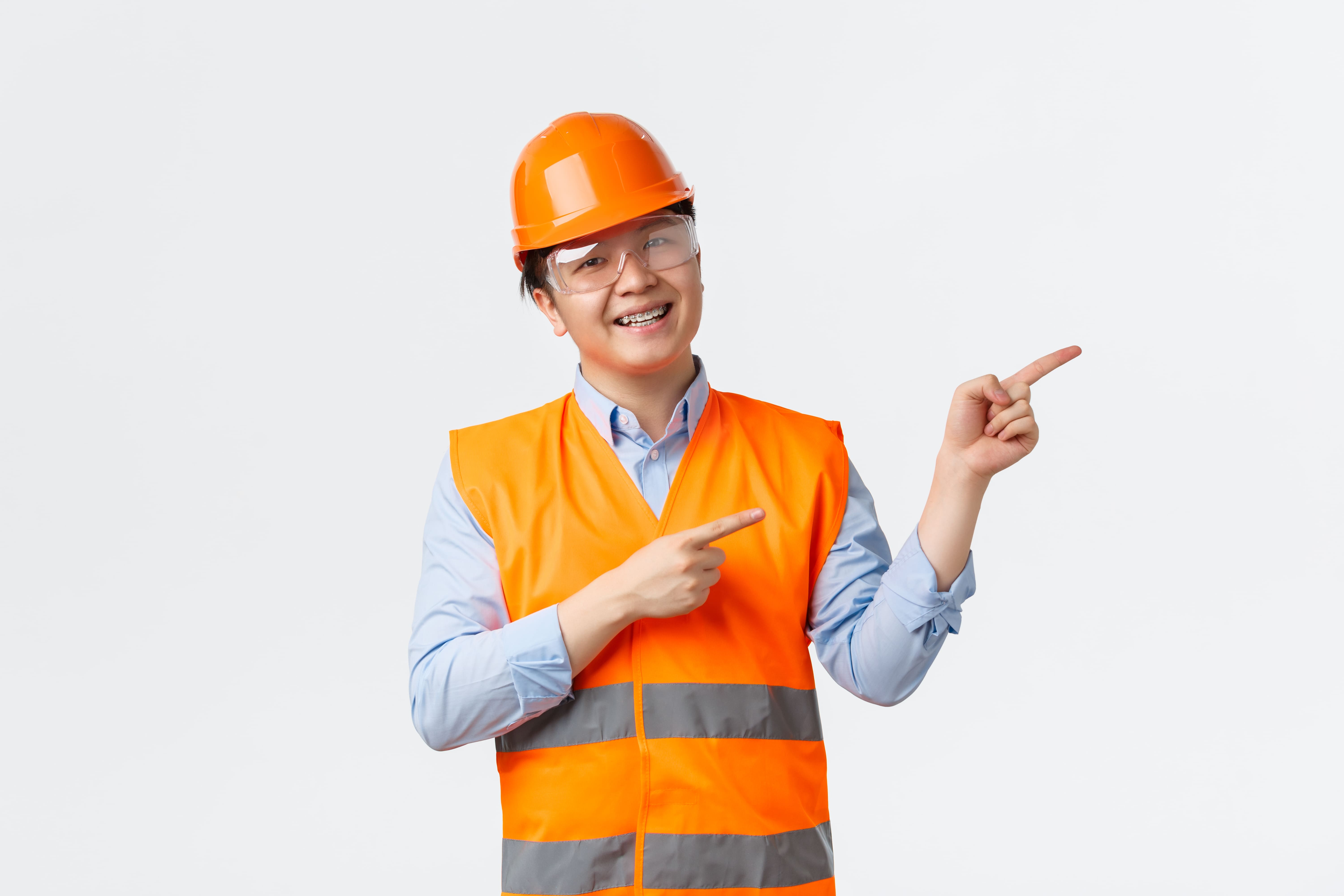
Pentingnya Manajemen Fatigue di Perusahaan Tambang dan Regulasi Kecukupan Jam Tidur
Workplace safety is a crucial aspect of any business operation. Ensuring that employees work in a secure environment is not only a moral obligation but also a legal one. Despite all preventive measures, workplace accidents still occur, leading to injuries, loss of productivity, and, in severe cases, even fatalities. Understanding the nature of these accidents, their types, and the methods to prevent them is key to fostering a safer working environment.
A workplace accident is an unforeseen and unplanned event that occurs in the workplace, leading to injury, illness, or even death. These accidents can result from a variety of factors, including unsafe working conditions, human error, mechanical failures, or a combination of these. The consequences of workplace accidents extend beyond the immediate physical harm to employees; they can also have significant financial implications for businesses, including medical costs, compensation claims, legal fees, and loss of productivity.
Workplace accidents come in many forms, each with its own causes and prevention strategies. Below are some of the most common types of accidents that occur in various industries:
One of the most frequent types of workplace accidents, slips, trips, and falls can happen in any industry. These accidents often result from wet floors, uneven surfaces, poor lighting, or misplaced objects. Injuries from such accidents range from minor bruises to severe fractures or head injuries.
Machinery accidents occur when workers operate heavy machinery without proper training or when safety protocols are not followed. These accidents can lead to severe injuries, including amputations, crushing injuries, or even death.
Accidents involving falling objects are common in construction sites and warehouses. Improperly secured tools, materials, or equipment can fall from heights, causing significant injuries to workers below.
Electrical accidents are particularly dangerous as they can lead to burns, shocks, or electrocution. These accidents often occur due to faulty wiring, exposed electrical components, or improper use of electrical equipment.
In industries where hazardous chemicals are used, accidental exposure can lead to poisoning, chemical burns, or respiratory problems. Such accidents are typically the result of improper handling, storage, or disposal of chemicals.
Fatigue-related accidents are a serious concern in industries that require long working hours, shift work, or high levels of concentration. Fatigue impairs cognitive function, slows reaction times, and increases the likelihood of errors, making it a significant risk factor for workplace accidents.
Fatigue is a state of physical and mental exhaustion that can severely impact a worker's ability to perform their duties safely. When an employee is fatigued, their judgment, coordination, and alertness are compromised, leading to an increased risk of accidents. In some industries, such as mining, transportation, or healthcare, fatigue can be particularly dangerous, as the work often involves operating heavy machinery, driving long distances, or making critical decisions.
Fatigue-related accidents can occur in various forms, including:
Vehicle Collisions: Fatigued drivers have slower reaction times and are more likely to fall asleep at the wheel, leading to accidents.
Machinery Mishaps: Fatigued workers operating machinery may make errors in judgment or fail to follow safety protocols, resulting in accidents.
Human Errors: Fatigue can cause workers to overlook important details, leading to mistakes that can have serious consequences.
Given the significant risks associated with fatigue, it is essential for employers to take proactive measures to manage and prevent fatigue-related accidents.
Preventing workplace accidents requires a comprehensive approach that includes risk assessment, employee training, and the implementation of safety protocols. Here are some effective strategies for preventing common workplace accidents:
Regular risk assessments are crucial for identifying potential hazards in the workplace. Employers should evaluate the work environment, equipment, and processes to identify risks and implement measures to mitigate them.
Employees should receive proper training on how to perform their tasks safely, including the correct use of machinery and equipment, handling of hazardous materials, and emergency procedures. Regular refresher courses should also be provided to ensure that employees remain aware of safety protocols.
Keeping the workplace clean and organized can prevent accidents such as slips, trips, and falls. Ensure that walkways are clear of obstructions, spills are promptly cleaned up, and tools are stored properly.
Safety protocols should be established and enforced across the workplace. This includes wearing appropriate personal protective equipment (PPE), following lockout/tagout procedures, and adhering to safety guidelines when operating machinery.
Employees should be encouraged to report any potential hazards or unsafe conditions to their supervisors. Prompt reporting allows for quick action to address the issue before an accident occurs.
One of the most effective ways to prevent fatigue-related accidents is by implementing a Fatigue Management System (FMS). An FMS is a comprehensive approach to managing worker fatigue by monitoring and controlling the factors that contribute to fatigue. It typically involves the use of technology, such as wearables, to track sleep patterns, work hours, and signs of fatigue in real-time.
Fatigue Management Systems (FMS) play a crucial role in preventing fatigue-related accidents by identifying and mitigating the risks associated with worker fatigue. An effective FMS includes the following components:
Monitoring and Assessment: Wearable devices and software can monitor workers' sleep patterns, alertness levels, and overall well-being. This data can be used to assess the risk of fatigue and take preventive action.
Work Schedule Optimization: An FMS can help optimize work schedules to ensure that employees have adequate rest periods and are not working excessively long hours. This reduces the likelihood of fatigue and improves overall safety.
Real-Time Alerts: Fatigue Management Systems can provide real-time alerts to both workers and supervisors when signs of fatigue are detected. This allows for immediate intervention, such as taking a break or adjusting the workload.
Education and Training: An FMS can also include educational resources and training programs to help employees understand the importance of managing fatigue and how to do so effectively.
Data-Driven Decisions: By collecting and analyzing data on worker fatigue, companies can make informed decisions about staffing, scheduling, and safety protocols. This proactive approach helps prevent accidents before they occur.
Workplace accidents are a significant concern for businesses across all industries. Understanding the different types of accidents, including those related to fatigue, is essential for implementing effective prevention strategies. By conducting regular risk assessments, providing proper training, and implementing a comprehensive Fatigue Management System, employers can create a safer working environment, reduce the risk of accidents, and protect the well-being of their employees.
Pentingnya Manajemen Fatigue di Perusahaan Tambang dan Regulasi Kecukupan Jam Tidur
Bahaya Kelelahan di Lingkungan Kerja: Faktor Penyebab dan Solusinya
Kecelakaan Kerja Akibat Fatigue: Pengertian, Penyebab, dan Solusi Pencegahannya
Peran Fatigue Management dalam Mengurangi Risiko Kecelakaan Akibat Mengantuk
Pentingnya Manajemen Fatigue di Perusahaan Tambang dan Regulasi Kecukupan Jam Tidur
Bahaya Kelelahan di Lingkungan Kerja: Faktor Penyebab dan Solusinya
Kecelakaan Kerja Akibat Fatigue: Pengertian, Penyebab, dan Solusi Pencegahannya
Peran Fatigue Management dalam Mengurangi Risiko Kecelakaan Akibat Mengantuk